Una revisión del modelado matemático de celdas de combustible de membrana de intercambio de protones y de metanol directo
Introducción
Se ha puesto mucho énfasis en el desarrollo de fuentes de energía duraderas, eficientes y portátiles para seguir mejorando la tecnología en dispositivos electrónicos comerciales, equipos de diagnóstico médico, comunicaciones móviles y aplicaciones militares. Todos estos sistemas requieren que la fuente de energía sea liviana, eficiente desde el punto de vista energético y capaz de funcionar durante largos períodos de tiempo sin necesidad de recargar combustible. Los sistemas de energía más populares hoy en día consisten en baterías desechables alcalinas, de zinc-carbono o de dióxido de azufre y litio, o baterías recargables de plomo-ácido, níquel-cadmio o iones de litio. Los pequeños dispositivos actuales, como teléfonos móviles y ordenadores portátiles, utilizan baterías pesadas, costosas y que deben recargarse o desecharse con frecuencia. Además, las mejoras tecnológicas en la electrónica comercial se están desacelerando debido a la falta de fuentes pequeñas de alta energía para sostener las nuevas funciones durante largos períodos de tiempo. Reducir el tamaño de la pila de combustible y aumentar el rendimiento permite que las tecnologías sean más avanzadas debido a que hay más espacio en el dispositivo para la electrónica.
El ejército tiene una necesidad única de alimentar dispositivos portátiles que actualmente funcionan con baterías. Actualmente se están desarrollando dispositivos para el casco de un soldado, la radio en el casco del soldado, la computadora alrededor de su cintura, la mira del arma en su rifle, el sistema de visión nocturna, etc. Todos estos dispositivos tienen baterías, lo que agrega peso al soldado. reduciendo su movilidad y agilidad. Esto aumenta la agilidad, la resistencia y la capacidad de supervivencia del soldado. El tamaño también es importante. Reducir el tamaño de la pila de combustible permite al soldado llevar más artículos en su mochila. El soldado actual carga con 16 baterías diferentes, que pesan aproximadamente 2,5 cada una. El objetivo del futuro soldado es tener un máximo de 4 baterías con menos de 2,0 libras de peso y al mismo tiempo mantener >1 kW de potencia en una misión de 72 horas. Las opciones actuales no son viables para aplicaciones portátiles porque son pesadas, poco prácticas y no cumplen con los requisitos de energía actuales.
Las pilas de combustible son conocidas por su alta densidad de energía, una variedad de fuentes de combustible y su facilidad de ampliación para requisitos específicos de aplicaciones. Las pilas de combustible con membranas de electrolitos poliméricos han sido históricamente atractivas debido a su funcionamiento a baja temperatura y su construcción relativamente simple. Con el aumento de la atención hacia las tecnologías MEMS, a finales de la década de 1990 se inició la investigación sobre la miniaturización de las pilas de combustible. La mayor parte del trabajo hasta la fecha ha consistido en miniaturizar las tecnologías más grandes existentes sin aprovechar las técnicas de microfabricación y procesamiento MEMS, o las ventajas del flujo de fluidos a microescala. Se han realizado algunos experimentos utilizando obleas de silicio, técnicas de fotolitografía, etc., pero sin pensar mucho en cuáles podrían ser los diseños óptimos para las pilas de combustible a microescala. Esta publicación revisa el trabajo que se ha realizado sobre micropilas de combustible y describe modelos matemáticos relevantes en la literatura.
Las pilas de combustible de membrana de electrolito polimérico (PEM) convencionales constan de dos electrodos catalizadores (el ánodo y el cátodo) separados por un electrolito polimérico. Los combustibles gaseosos se alimentan continuamente al ánodo (electrodo negativo), mientras que un oxidante (oxígeno del aire) se alimenta continuamente al cátodo (electrodo positivo). En los electrodos tienen lugar reacciones electroquímicas para producir una corriente eléctrica. En la Figura 1 se muestra una representación esquemática de una pila de combustible de metanol directo (DMFC), que es un tipo de pila de combustible PEM.

Figura 1. Celda de combustible de alimentación líquida de metanol directo (DMFC)
Históricamente, la pila de pilas de combustible PEM está formada por celdas repetidas separadas por placas bipolares. Aumentar el número de celdas en la pila aumenta el voltaje, mientras que aumentar el área de superficie de las celdas aumenta la corriente. La Figura 2 muestra una representación de una pila de pila de combustible tradicional.
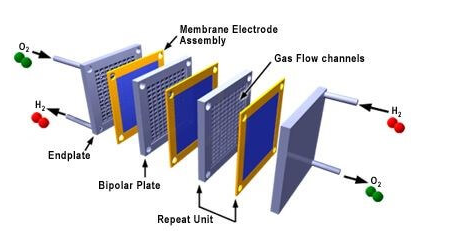
Figura 2. Vista en despiece de una pila de pila de combustible con membrana de electrolito polimérico. (Imagen:3M1)
El DMFC se desarrolló para abordar los problemas de almacenamiento de combustible de hidrógeno y eliminar la necesidad de un reformador para convertir el metanol en hidrógeno para que funcione una pila de combustible de hidrógeno. La DMFC se clasifica como pila de combustible de membrana de intercambio de protones (PEMFC) porque también utiliza una membrana PEM. Sin embargo, además del platino, se deben agregar otros catalizadores como el rutenio (Ru) para romper el enlace metanol en la reacción anódica.
Los principales obstáculos para las pilas de combustible de metanol directo son: (1) el secado de la membrana (especialmente a altas temperaturas), (2) el cruce de metanol del ánodo al cátodo a través del separador de membrana, (3) las pérdidas por despolarización en el cátodo debido al cruce de metanol, (4) método eficiente de distribución de metanol y aire a microescala, (5) altos costos de los materiales de la pila de pilas de combustible y (6) diseño de sistemas. Todos estos problemas están presentes en las pilas de combustible basadas en MEM (muchos en menor medida), pero existe una necesidad adicional de disminuir el espesor de las pilas de combustible. Muchas micropilas de combustible utilizan hasta la fecha la membrana de intercambio de protones tradicional (como Nafion®), pero el tamaño de la pila de combustible está muy limitado por este factor.
Materiales PEMFC y DMFC
Dado que las DMFC son una tecnología nueva en comparación con otras pilas de combustible, es necesario abordar una serie de problemas para que el sistema DMFC sea una tecnología viable para aplicaciones comerciales y militares. Los DMFC deben volverse más compactos, livianos, rentables y deben satisfacer las demandas de energía de las aplicaciones comerciales y militares. Los DMFC serán más compactos, livianos y rentables cuando se seleccionen nuevos materiales y procesos. Los principales componentes que deben mejorarse son la membrana polimérica, los electrodos, las placas bipolares y el subsistema de alimentación de metanol.
3.1 Estructura de intercambio de polímeros
La membrana conductora de protones suele estar formada por una estructura polimérica basada en PTFE, a la que están unidos grupos de ácido sulfónico (p. ej. Nafion 112, 115, 117). Las moléculas de ácido están fijadas al polímero y no pueden escaparse, pero los protones pueden migrar libremente a través de la membrana. La membrana polimérica suele tener un tamaño de 175 micras, pero también hay muchas membranas poliméricas disponibles comercialmente que tienen un espesor inferior a 175 micras. Con frecuencia se utilizan membranas de 50 micrones o menos de espesor, pero son ligeramente inestables (químicamente) y no han sido tan eficientes para conducir protones en el DMFC.
La integración de Nafion en micropilas de combustible es difícil porque se hincha durante el funcionamiento, lo que lo hace incompatible con Nafion. Las microtecnologías y nanotecnologías hacen posible la fabricación de membranas nanoporosas. Se han realizado estudios con varios conceptos para la estructura de intercambio de protones en micropilas de combustible [3]:
1. Nanoporous membrane
2. Nanochannels in silicon
3. Liquid electrolyte confined in a microchannel network
Estas configuraciones eliminan el cruce de metanol que ocurre en las membranas tradicionales, permiten que la celda de combustible funcione a temperaturas más altas y son menos costosas para la producción en masa.
3.2 Los electrodos
Los electrodos suelen estar hechos de una mezcla porosa de platino soportado sobre carbono o platino/rutenio. Para catalizar reacciones, las partículas del catalizador deben tener contacto con los conductores protónicos y eléctricos. También debe haber pasajes para que los reactivos lleguen a los sitios del catalizador y para que salgan los productos de la reacción. El punto de contacto de los reactivos, el catalizador y el electrolito se denomina convencionalmente interfaz trifásica. Para lograr velocidades de reacción aceptables, el área efectiva de los sitios del catalizador activo debe ser varias veces mayor que el área geométrica del electrodo. Por lo tanto, los electrodos se hacen porosos para formar una red tridimensional, en la que se ubican las interfaces trifásicas.
El espesor de los electrodos en las pilas de combustible tradicionales suele ser de 250 a 2000 angstroms con una carga de catalizador de entre 0,2 y 0,5 mg/cm2. Para las micropilas de combustible, la carga típica de platino es de 5 a 60 nm de espesor. Se deposita una capa de adhesión antes de la capa de catalizador, y normalmente tiene un espesor de 25 a 300 angstroms. La carga de catalizador es un factor limitante de costes para el DMFC. El costo de la pila de DMFC se reduciría si se disminuye la cantidad de platino, se combina con ella otro elemento (más barato), se reemplaza el platino con otro elemento o se miniaturiza la pila de combustible hasta el punto en que el catalizador no tiene un coste tan prohibitivo.
3.2.1 Capa de difusión
La capa de difusión está hecha de materiales porosos eléctricamente conductores, como papel carbón o Toray. La conductividad del papel se puede mejorar llenándolo con polvo eléctricamente conductor, como negro de carbón. Para ayudar a eliminar el agua de los poros del papel carbón, la capa de difusión se puede tratar con PTFE. Algunos desarrolladores de micropilas de combustible renuncian por completo a la capa de difusión y el platino se pulveriza directamente sobre la estructura de intercambio de protones.
Placas de campo de flujo PEMFC y DMFC
3.3 Placas bipolares
En la pila de pilas de combustible, las placas bipolares separan los gases reactivos de las pilas adyacentes, conectan las pilas eléctricamente y actúan como estructura de soporte. Las placas bipolares tienen canales de flujo de reactivos en ambos lados, formando los compartimentos anódico y catódico de las celdas unitarias en los lados opuestos de la placa bipolar.
La geometría del canal de flujo afecta las velocidades de flujo de los reactivos, la transferencia de masa y el rendimiento de la celda de combustible. Los materiales de placas bipolares deben tener una alta conductividad y ser impermeables a los gases. El material también debe ser resistente a la corrosión y químicamente inerte debido a la presencia de gases reactivos y catalizadores.
La mayoría de las placas bipolares tradicionales están hechas de acero inoxidable o grafito. Las placas de acero inoxidable son componentes pesados de un sistema de energía portátil. Las placas de grafito sólido son altamente conductoras, químicamente inertes y resistentes a la corrosión, pero son caras, quebradizas y costosas de fabricar. Los canales de flujo se mecanizan tradicionalmente o se graban electroquímicamente en las superficies de la placa bipolar de grafito o acero inoxidable. Estos materiales no son adecuados para la producción en masa y no funcionarían para un sistema de pila de combustible basado en MEMS debido a la incapacidad de trabajar con estos materiales a nivel de microescala. Los materiales típicos que se han utilizado en las pilas de combustible MEM son silicio, papel carbón y láminas metálicas finas, y se están empezando a utilizar técnicas tradicionales de microfabricación con las pilas de combustible MEMS.
3.31 Canales de flujo
En las celdas de combustible PEM, el campo de flujo debe diseñarse para minimizar la caída de presión (reduciendo los requisitos de bombas parásitas), al tiempo que proporciona una transferencia de masa adecuada y uniformemente distribuida a través de la capa de difusión de carbono hasta la superficie del catalizador para la reacción. Las tres configuraciones de canales más populares para las pilas de combustible tradicionales son: 1) flujo serpentino, 2) paralelo y 3) flujo interdigitado. Algunas pilas de combustible de pequeña escala no utilizan un campo de flujo para distribuir el hidrógeno y/o el aire, sino que dependen de procesos de difusión del medio ambiente. Dado que la reacción del hidrógeno no limita la velocidad y puede ocurrir un bloqueo de agua en el ánodo humidificado, generalmente se usa una disposición en serpentina para el ánodo en celdas de combustible PEM más pequeñas.
El rendimiento de la pila de combustible mejora a medida que aumenta la velocidad del flujo de gas del canal, ya que el aumento de la velocidad del flujo mejora el transporte de masa. Al investigar el efecto de la geometría de la pila de combustible, es necesario considerar los siguientes parámetros geométricos: el patrón del canal de flujo, la forma del canal y de las nervaduras y el espesor de la capa de difusión, así como muchos otros factores. La velocidad en el canal de flujo aumentará a medida que disminuya el tamaño de la característica. Sin embargo, un inconveniente del tamaño de característica más pequeño es la mayor caída de presión en los canales de flujo.
3.311 Canales de Flujo Interdigitados
El flujo de reactivo para el diseño interdigitado es paralelo a la superficie del electrodo. A menudo, los canales de flujo no son continuos desde la entrada de la placa hasta la salida de la placa. Los canales de flujo tienen un final sin salida, lo que permite que el flujo de reactivo sea forzado bajo presión a atravesar la capa de reactivo poroso para llegar a los canales de flujo conectados al colector de la chimenea. Este diseño puede eliminar el agua de forma eficaz de la estructura del electrodo, lo que evita inundaciones y mejora el rendimiento. El campo de flujo interdigitado es bueno ya que el gas fue forzado hacia la capa activa de los electrodos donde la convección forzada evita inundaciones y limitaciones en la difusión del gas.

Figura 3: Diseño del campo de flujo interdigitado
Se han investigado los efectos de escala para celdas de combustible MEMS [1] en tamaños de características de 5 a 1000 micrones. Las velocidades de flujo en los canales individuales son inversamente proporcionales al tamaño de la característica. El rendimiento de la celda aumenta hasta que el tamaño de la característica se reduce a 500 micrones, pero el rendimiento comienza a disminuir por debajo de este tamaño. El rendimiento de la celda comienza a aumentar nuevamente cuando el tamaño de la característica es de 50 micrones o menos [1]. La pérdida por caída de presión supera el aumento de potencia máxima en canales de menos de 50 micras.
3.312 canales serpentinos
La trayectoria del flujo serpentino es continua de principio a fin. Una ventaja del camino de flujo serpentino es que cualquier obstrucción en el camino no bloqueará toda la actividad aguas abajo de la obstrucción. Una desventaja del flujo serpentino es el hecho de que el reactivo se agota a lo largo del canal, de modo que se debe proporcionar una cantidad adecuada de gas para evitar pérdidas de polarización excesivas. Cuando se utiliza aire como oxidante, normalmente hay problemas con la distribución del flujo de gas del cátodo y la gestión del agua de la celda. Cuando la pila de combustible funciona durante largos períodos de tiempo, el agua formada en el cátodo se acumula en el cátodo. Se requiere una fuerza para sacar el agua de los canales. Este diseño es relativamente eficaz para proporcionar distribución de flujo a través de la superficie del electrodo de la pila de combustible. Sin embargo, este diseño puede causar una gran pérdida de presión debido al recorrido de flujo relativamente largo.

Figura 4: Diseño del campo de flujo serpentino
En las pilas de combustible MEMS, la velocidad del flujo es inversamente proporcional al cuadrado de los tamaños de las características. Los canales serpentinos pueden tener el efecto de incrustación más pronunciado que otros patrones de flujo. Se obtiene un mejor rendimiento entre tamaños de características de 483 a 99 micrones, pero las pérdidas de presión por debajo de 200 micrones son tan grandes que también anula el efecto de la reducción de escala [1]. Al igual que en los canales interdigitados, el mayor rendimiento en canales más pequeños se debe al aumento de la convección y a la reducción de la zona muerta. La caída de presión es alta en los canales serpentinos porque la velocidad del flujo aumenta con el cuadrado del tamaño de la característica y la longitud del canal es inversamente proporcional al tamaño de la característica. En [20], el campo de flujo serpentino produjo un rendimiento mucho mayor que el campo de flujo paralelo, especialmente a altas densidades de corriente. Se plantea la hipótesis de que cuanto mayor sea el número de Reynold, mayor será la transferencia de masa desde el canal de flujo a la capa de difusión de gas. Cuando la profundidad del canal se redujo de 1 mm a 300 micrones, el rendimiento de la densidad de potencia aumentó en un 71,9% [20]. Cuando la profundidad del canal se redujo aún más a 100 micrones, el rendimiento disminuyó un 8,6% [20].
Configuraciones de pila PEMFC y DMFC
5.1 Configuración de la pila
Una pila de pilas de combustible tiene muchas pilas apiladas de modo que el cátodo de una pila está conectado al ánodo de la siguiente. Los componentes principales de la pila de combustible son los conjuntos de electrodos de membrana (MEA), juntas, placas bipolares con conexiones eléctricas y placas terminales. La pila está conectada mediante pernos, varillas u otro método para sujetar las celdas entre sí. Los aspectos clave del diseño de pilas de combustible:
• Distribución uniforme de reactivos en la celda.
• Distribución uniforme de reactivos dentro de la celda.
• Mantenimiento de la temperatura requerida en el interior de cada celda.
• Pérdidas resistivas mínimas
• Sin fugas de gas
• Robustez mecánica
La configuración de celda de combustible más común se muestra en la Figura 2. Cada celda (MEA) está separada por una placa con campos de flujo en ambos lados para distribuir el combustible y el oxidante. Las placas finales de la pila de pilas de combustible tienen sólo un campo de flujo de un solo lado. La mayoría de las pilas de pilas de combustible, independientemente del tipo, tamaño y combustible utilizados, tienen esta configuración.
La mayoría de los sistemas MEMS utilizan silicio como material preferido debido a la disponibilidad, el bajo costo y las diversas tecnologías de procesamiento disponibles. Algunos de los procesos normalmente utilizados para crear micropilas de combustible son el grabado anisotrópico, el grabado de iones reactivos profundos (DRIE) y la deposición de diversos materiales mediante CVD y PVD. También se están empezando a utilizar polímeros, pero los sistemas de silicio/vidrio son mecánicamente más estables, pueden resistir altas temperaturas/presiones y son básicamente químicamente inertes. Sin embargo, el silicio es frágil y los polímeros permiten configuraciones y técnicas de procesamiento alternativas. Algunos de los polímeros que se están investigando incluyen PMMA y PDMS mediante grabado iónico, micromecanizado de superficies poliméricas, estampado en caliente, litografía suave y mecanizado láser. También se están investigando láminas de acero inoxidable y películas de cobre como materiales para placas colectoras de corriente y de suministro de combustible [3].

Figura 7. Micropila de combustible básica basada en el diseño de pila de combustible tradicional
Modelos PEMFC y DMFC
Las mejoras necesarias para el rendimiento y funcionamiento del DMFC exigen un mejor diseño, materiales y optimización. Estas cuestiones sólo pueden abordarse si se dispone de modelos de procesos matemáticos realistas. Hay muchos modelos publicados para pilas de combustible PEM, pero sólo un pequeño número para DMFC. La Tabla 1 muestra una comparación de publicaciones recientes que describen las características clave de los modelos matemáticos.
La primera columna de la Tabla 1 muestra la referencia de cada modelo matemático. La segunda columna resume si el modelo era dinámico o de estado estacionario. Las siguientes siete columnas presentan la dimensionalidad de las capas del DMFC tradicional. Un «0» significa que el parámetro se describe mediante un modelo de parámetros agrupados y un «1» significa que el componente se modeló en 1-D. Las siguientes dos columnas de la Tabla 1 presentan el tipo de expresión cinética del electrodo. En la mayoría de los modelos 1D se utilizan expresiones simples de tipo Tafel. Sólo unos pocos artículos utilizan expresiones de tipo Butler-Volmer, y algunos otros modelos utilizan una cinética de reacción de varios pasos más realista y compleja para el método electroquímico de oxidación de metanol. Las dos columnas siguientes comparan las fases utilizadas para las estructuras de ánodo y cátodo. Es bien sabido que coexisten 2 fases (líquido y gaseoso) bajo una variedad de condiciones de operación. En el lado del ánodo se produce dióxido de carbono en la capa de catalizador, especialmente a temperaturas elevadas. Dentro de la estructura del cátodo, el agua puede condensarse y bloquear el camino para que el oxígeno fresco llegue a la capa del catalizador.

BV: Butler-Volmer, dc: coeficiente de resistencia; dyn: dinámico, eff:efectivo, F: Fick’s, G: gas, irrev: irreversible, L: líquido, MS: Maxwell-Stefan dinámico, NP: Nerst-Plank, S: Schlogl,
SD: difusión superficial, SS: estable estado, TD: termodinámica
Capas DMFC: A: Compartimiento anódico/canales de flujo, AD = Capa de difusión anódica, AC = capa catalizadora anódica, M = membrana/PEM, CC = capa catalizadora catódica, CD = capa de difusión catódica, C = Compartimento catódico/canales de flujo ** Un «0» significa que el parámetro se describe mediante un modelo de parámetros agrupados y un «1» significa que el componente se modeló en 1-D.
Una característica importante de cada modelo son las descripciones de transporte de masa del ánodo, cátodo y membrana de intercambio de polímero. Son varios los modelos de transporte masivo que se utilizan. Los modelos de difusión de Fick simple (F) y los modelos de difusión de Fick efectiva (eff F) suelen utilizar coeficientes de transporte efectivo determinados experimentalmente en lugar de difusividades de Fick y no tienen en cuenta las contribuciones del flujo convectivo. Por lo tanto, muchos modelos utilizan expresiones de transporte de masa de Nerst-Planck (NP) que combinan la difusión de Fick con el flujo convectivo. El flujo convectivo normalmente se calcula a partir de la Ley de Darcy utilizando diferentes formulaciones del coeficiente de permeabilidad hidráulica. Algunos modelos utilizan las formulaciones de Schlogl (S) para el flujo convectivo en lugar de la ley de Darcy, que también tiene en cuenta el flujo electroosmótico y puede usarse para el transporte de masa dentro del PEM. Un método muy simple para incorporar flujo electroosmótico en la membrana es aplicar modelos de coeficiente de arrastre (dc), que supone una proporción de flujo convectivo de agua y metanol con respecto al flujo de protones. Otro tipo popular de descripción del transporte masivo es la formulación de Maxwell-Stefan para mezclas de múltiples componentes. Esto se ha utilizado para el transporte en fase gaseosa, pero esta ecuación sería mejor utilizada para el transporte de masa en fase líquido-vapor. Sólo un modelo reciente utiliza esto para ambas fases. Rara vez se utilizan modelos de difusión superficial y modelos derivados de la termodinámica irreversible (irrev. TD). Los modelos de transporte masivo que utilizan coeficientes de transporte efectivos y coeficientes de arrastre (F, eff F, NP, S) generalmente solo producen buenas aproximaciones a los datos experimentales bajo un rango limitado de condiciones operativas.
La penúltima columna de la Tabla 1 presenta si se tiene en cuenta el hinchamiento de la membrana PEM. La mayoría de los modelos asumen un PEM completamente hidratado. En un caso [51], la absorción de agua se describe mediante una correlación empírica, y en [52 – 54] se utiliza un modelo termodinámico (TD) basado en el cambio de energía libre de Gibbs dentro del PEM en función del contenido de agua. La última columna indica si el modelo publicado incluye balances de energía. Obviamente, todos los modelos que asumen un funcionamiento de celda isotérmica no tenían balances de energía incluidos.
Conclusión
Las pilas de combustible de membrana de intercambio de protones y de metanol directo se encuentran entre las tecnologías de pilas de combustible más prometedoras hasta la fecha. Se prevé que las pilas de combustible de metanol directo (DMFC) serán la fuente de energía elegida para futuras aplicaciones portátiles. El bajo costo del metanol, la alta densidad energética y la seguridad inherente explican el inmenso interés en esta fuente de energía. Uno de los principales retos técnicos del DMFC es el desarrollo de un modelo matemático para una micropila de combustible directa de metanol que ayudará a optimizar, diseñar y fabricar futuras micropilas de combustible. Las pilas de combustible MEMS son un campo relativamente nuevo en el que las pilas de combustible más grandes se han miniaturizado en su mayoría. El desarrollo de estos modelos micro DMFC conducirá a micropilas de combustible de metanol directas mejoradas sin las membranas tradicionales que pueden ayudar a hacer realidad la tecnología de micropilas de combustible más rápidamente.
